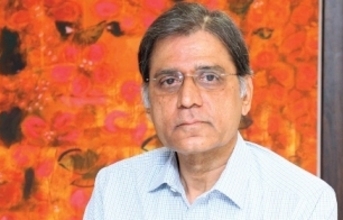
B K Rajkumar, Executive Vice President-Business Excellence at Godrej & Boyce Mfg. Co. Ltd.
Successful manufacturing companies are always driven by the quest to continuously improve on what they are doing. They are guided by questions like "How can we improve this?" or "Is there a better way of doing this?". And more often than not, these improvements are initiated by the operators on the shopfloors.
These proactive operators not only enhance their own efficiency but also contribute to the Company's profitability with simple yet effective solutions. Many of these useful ideas result from trouble-shooting or problem solving addressed at day-to-day operational issues.
In the manufacturing parlance, this activity is often described as kaizen. Kaizen is actually a Japanese term where ‘kai' means change and ‘zen' means good, so together it means a good change or improvement. However, today the term - as a business process - means ‘continuous improvement'. And it is practiced not just by manufacturing professionals but also general business professionals.
A quick example |
(Continued on the next page)