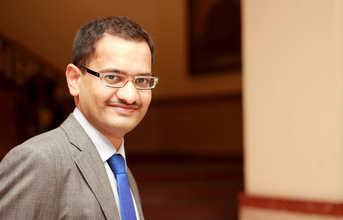
While most Indian SMEs have been adversely impacted by the slowdown, Pune based ElectroMech has been sailing through the challenging times with flying colours. "Not only have we managed to maintain our top line but have also improved our bottom lines by revamping the processes and making operations leaner," says Tushar Mehendale, Managing Director, ElectroMech, which is a leading manufacturer of industrial cranes. Of course, he does mention that on account of the infamous ‘policy paralysis' the growth of the capital goods industry has been affected in the country. "The last two years were particularly painful in terms of new business," he adds.
Of course, he is not new to challenges. ElectroMech was actually started by his father many years back along with a few technocrat friends. But it was a very small scale firm with no significant presence in the market place. Things were only getting worse when Tushar had returned with a degree from the US. But he took charge of things; studied the market and started filling the gaps by providing quality products. And it paid off. So from a small company engaged in supplying cranes to local customers doing an annual turnover of Rs3.25 crore with around 70 people, today ElectroMech generates a revenue of more than Rs200 crore and employs more than 500 people.
Focus on quality
How did this happen? A big focus on quality, says Tushar. And this needs proper planning and huge efforts. "At ElectroMech we have implemented a lean manufacturing system that ensures that during handover from one component of the values stream to another, the handover is complete in all respects and meets the specified requirements," he says. Basically, a lot of emphasis is placed on self certification by the respective process owners.
In case of any issues that arise due to incomplete or improper work, the root cause analysis is done in a systematic manner and the system is tweaked to ensure that the incident will not repeat again. This way the quality system runs in a self correcting mode and ensures continuous improvement. "Higher accountability and higher ownership lead to greater employee participation in the system and this leads to an overall pride that the employee feels for his / her own work. This way quality becomes personal for the respective employee and greater levels of quality are thus achieved."