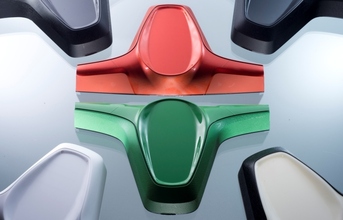
The DirectCoating process produces a component in just one step. After production in the injection mold, the plastic substrate is then transferred to a second, minimally larger cavity, into which the coating system is injected via a reaction injection molding (RIM) mixing head. This creates a polyurethane (PU) coated component with outstanding properties that requires virtually no post-processing.
"Compared with the conventional process, the integrated process offers substantial savings potential with respect to logistics effort, energy consumption and space requirements," said automotive coatings expert Dr. Jan Weikard. "All you need is an injection molding machine and a RIM system."
END