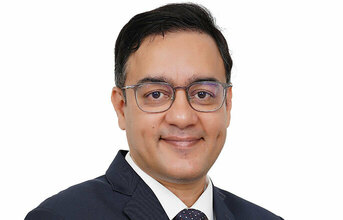
What steps is Milacron taking in India to support the ‘Make in India' initiative?
We have several initiatives in place to lend our contribution to the Make in India and Make for the World. For one, we are increasing our localised manufacturing, which will stimulate the growth of indigenous production capabilities. Additionally, we look forward to enhancing our manufacturing skills and quality processes, enabling Milacron India to increase global exports. Skill development is another area of focus. We continue to invest in Learning and Development (L&D), not just for our employees, but also regularly conduct Level 1 and Level 2 courses for the operations and maintenance teams of our customers. We also have the largest service team in India, enabling us to provide a same-day response to 90 per cent of our calls.
What are the key innovations in plastic processing in the automotive segment that the company is seeing now, and what further innovations do you see upcoming in the industry?
From my perspective, it's interesting to witness how plastics are revolutionising vehicle construction. Plastic components, weighing up to 100 kilogrammes, now make up approximately 10-15 percent of a vehicle's total weight. It appears that traditional sheet metal and steel in exterior parts like doors, fenders, and bumpers are being replaced by lightweight plastic counterparts.
The use of various plastics—such as polypropylene, polyurethane, polyamides, and PVC—extends across both interior and exterior elements, opening new design possibilities and enhancing overall quality. Notably, the industry is currently leaning toward the use of recyclable plastics and implementing structured recycling processes.
Looking ahead, future advancements in the industry will be focused on technologies like foaming, sandwich moulding, gas-assist moulding, advanced heat-cooling systems, and over-moulding. These innovations aim to achieve objectives like lightweighting, design flexibility, energy savings, improved aesthetics, and enhanced durability.
What strategies do you have in place for further growth, and what is the target that you see the company achieving by 2030?
Our goal is to ensure sustained growth for the company, and to achieve this, we have a well-defined plan of action. We place a strong emphasis on research and development (R&D), as well as digitalisation, to drive the development of advanced technologies. Additionally, we are pursuing collaborations and partnerships with industry leaders and exploring new markets to expand our product portfolio.
Through these initiatives, our vision for 2030 revolves around the triple A's: augmenting our manufacturing capacity, advancing our global presence, and achieving a substantial increase in revenue.