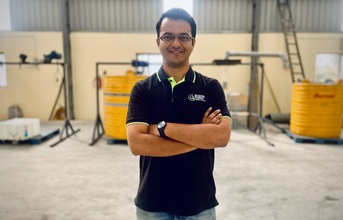
How is the market evolving for Battery recycling in India?
The battery recycling market in India has started to pick up pace now, just as the electric mobility space has over the past few years. There is a clear shift of focus to fight climate change, especially with the electrification of mobility and transitioning to renewable energy sources, which requires energy storage solutions at a large scale. As these markets expand, the lithium-ion batteries at the end of their life cycles will eventually be required to be recycled, slated to be a massive $30 billion market by the end of the decade.
What kind of demand are you receiving for Battery Swapping and Recycling?
Although many OEMs are looking at second-life applications of their lithium-ion batteries, like mobility to stationary storage, the usage is yet to prove its unit economics at scale. As a result, several companies are on the lookout for strategic partnerships with recycling companies, such as Metastable, to ensure that the waste batteries do not end up in dump yards but instead be recycled to establish the recycled metals as an alternative source of sustainable raw materials.
Where does India stand on the battery recycling front?
The lithium-ion battery recycling industry in India is at a very nascent stage today. As a country, we have taken notice of the global market potential and the urgent need to act for a greener future. However, India's total end-toend recycling capacity is not even close to the amount of waste batteries generated each day. The recycling industry has just started preparing itself for the oncoming wave of lithium-ion batteries reaching the end of their lifecycle from the first generation of the electric vehicles that have been in the market for a few years. This volume of waste is in addition to the already 70-100 metric tonnes of waste batteries from consumer electronic devices generated daily in India.
What kind of infrastructure do we have now here in India in terms of Battery recycling?
The total installed capacity of recycling lithium-ion batteries and its associated waste is nowhere close to what is required today and soon. The industry is over-saturated with companies processing waste batteries to separate black mass from the rest of the battery materials, which contains the most valuable metals of a Li-ion battery, namely lithium, nickel, and cobalt. Much of the value is lost here because this black mass is shipped to other countries for further refining. As a result, India is losing out on securing the supply of critical metals to achieve its goal of Net Zero by 2070. Therefore, there is a much need for eco-friendly, sustainable recycling technologies, such as Metastable's Integrated Carbothermal Reduction™ that can scale in tandem with the rising demand for lithium-ion battery applications like green mobility solutions, stationary energy storage and consumer electronics.
What kind of infrastructure is needed to recycle EV batteries in a greener way, and how can India emerge as the global hub for EV battery manufacturing and recycling?
The most prevalent recycling technologies of today are plagued with issues of scale and high operational expenditures. Both issues are primarily a result of highly chemical-intensive processes. That is why there is a need to find alternative solutions for extracting materials out of waste which is low on capital and operational expenditures while generating minimal waste during the process. One such technology, developed indigenously, is Metastable's Integrated Carbothermal Reduction™ (ICR). ICR is specifically designed to extract critical metals like lithium, cobalt, nickel, copper and aluminium out of waste batteries without any chemicals at costs that are practically a fraction of the current industry standards. The process design, along with low-cost structures, enables the ICR to be highly scalable and globally deployable to put India at the forefront of the sustainable battery manufacturing and recycling ecosystem.