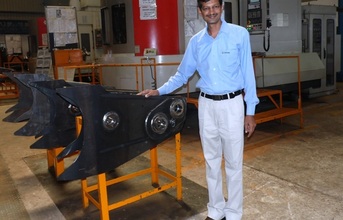
All these activities resulted in many positives. Stoppages in machines due to ‘no air after power trip' or ‘low air pressure' were reduced. Air cleaning points and air leakages also decreased and a 500 L air reservoir was added. General break downs were reduced and specific break downs were eliminated by implementing additional checks.
For example, the rejection of parts at the TAL 1 machine was eliminated by adding Air / Coolant blast during tool change to ensure chip removal between Boring Bar and Spindle Face.. Tool breakage on all BFW machines were eliminated by adding Hydraulic Counter Balance (BFW performed this activity on FOC Basis). The cutting tools order scheduling was modified to 10 percent extra discount. Milling cutter was acquired during yearly promotion sales.
Additionally, there was substantial savings in energy consumption: Power factor achieved 0.99 against 0.85 from June 2013, and air compressor leakage came down to 7 percent against earlier 34 percent (resulting in no machine stoppage). On time for TAL 1 reduced from 17 Min to 3 Min.
In Phase three (from October 2013 to August 2014), all RFQs were converted into orders. Innovative ideas were implemented with positive results. The loader tower manual operation (debarring) was reduced by 50 percent through Boring Bar Modification. Loader tower probing was implemented in Z Axis to eliminate Part Reference variation.
Seventy percent fork lift movement was reduced. "We managed to enhance the overall team competency level," says Agarwal. The efforts and achievements during this Phase also included combination fixtures implementation for machining Boom & Loader Arm new variants with existing model.
Loader Tower Rough Boring Bar added chamfering cartridge (No cycle time or cost increase as dead inserts used). Loader Tower depth variation reduced from 3 mm to 0.3 mm by implementation of Z Axis Probing (Auto Z Axis offset measurement). Rail trolleys were implemented for shifting of parts. "And importantly, outsourced services were minimised to give us further cost savings."
Of course, the journey had its own set of challenges. "The biggest challenge was merging different teams into one team. The second challenge was implementing a performance oriented approach against the routine work approach. But the journey of excellence brought all employees on a common platform. Working like a coach, I encouraged all team members to work towards one organisational goal. We overcame the challenges by changing our overall approach through the 3R concept (Respect, Recognition & Reward)," says Agarwal.
END