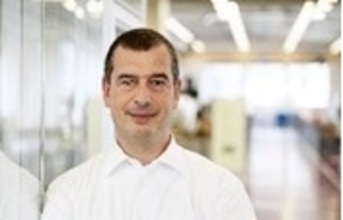
The new milling cutter is also intended to improve surface quality - how will it achieve this?
In this sector, a surface quality of approximately RZ 10 is usually required. We have achieved Rz 5 and have absolutely no problems fulfilling customer requirements with the system. This is possible thanks to the optimal cutting length of 4 mm, which applies a lower pressure.
These housings are very unstable because their walls are only between 2.5 mm and 3 mm thick. This quickly leads to vibration and, as a result, chatter marks. Up to now, there has always been a compromise between machining speed and surface quality. We can resolve this conflict.
Why have you chosen to use a fixed insert seat instead of the customary cartridge seat?
Adjusting the finishing inserts using the standard cartridge makes the tool more expensive and reduces the possible number of teeth. This ability to adjust the inserts is advantageous for standard applications of varying batch sizes because the tool can easily be modified to meet different conditions.
This flexibility is not necessary in the case of large quantities, however. For this reason, we decided to use the fixed insert seat. With the elimination of an adjustment step, it almost becomes a "Plug and Play" solution. In any case, we are required to manufacture the seats for the finishing inserts extremely precisely so that they all run exactly parallel to one another.
END
Source: Walter AG