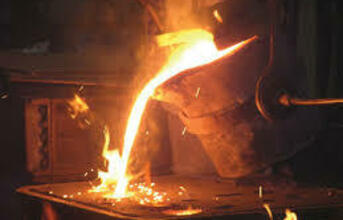
The strength of Indian Foundries lies in consistency, reliability, transparency & ability to produce engineered castings at competitive cost. India also has an advantage of large English speaking skilled workforce.
On the other hand, Chinese foundries have advantages of scale .There are various global players who have invested in China & have been operating there since last few decades.
But India has been a laggard in attracting investments in this sector and for that matter in other sectors too because of poor infrastructure, power availability, cumbersome and time consuming procedural delays, unpredictable business policies, labour laws etc.
With a lot of noise about government's "Make in India "initiative which promotes ease of doing business, there are various reforms, following which will enable the conversion of contingencies to reality.
Also the challenges faced by the exporters like high transaction costs, long transit and clearance time at ports etc needs to be addressed to strengthen exports and make India a global manufacturing hub.
Chinese foundries are increasingly becoming less competitive as the cost of power & labour is gradually increasing. Moreover, several buyers especially in India do not find it logical to import from China due to reliability, inconsistency and the cost of imports.
Even other overseas buyers are gradually shifting their outsourcing to India slowly. This opens immense opportunities for the Indian Foundries to capitalize on the positive sentiment of the industry.
There are only a few foundries in India which are medium and large scale units while a large number of units are operating at various operational levels. Compared to Indian Foundry Industry, Brazilian Foundry Industry is much smaller but it still has more units of large scale foundries (more than 100,000 Tons per annum production capacity).
Auto sector, as we all know is extremely cost sensitive and even the drive for ever increasing fuel efficiency & safety standards for the players in this sector cannot be compromised.
In order to meet the needs of the present Auto sector, foundries need to maintain infrastructure of the highest stature yet supply castings at competitive cost. Also there is a need to focus on scale, speed & sustainability along with continuous attention towards skilling the workforce.
While the government is striving to make policies, facilitate new investments and joint ventures with global players to improve infrastructure and ease of doing business, the industry should also look at bringing about transformation in various areas.
With the increased use of modern design and manufacturing tolls (including increased use of IT) and increased demand for goods with competitive costs and improved response time, the industry must focus on automation, scaling up operations, and also add value by producing ready to use finished castings & sub assemblies to meet the demands for ever changing auto industry.
(Continued on the next page)