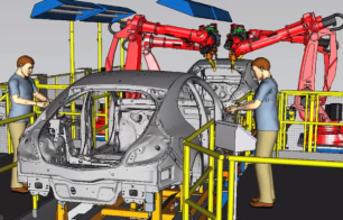
The age of Automation
In the past, manufacturing in India signified a large production volume, low-level technology and cheap labour - a fact that is no longer true. The increase in domestic demand, evolving consumption patterns, the advent of emerging technologies and fast changing infrastructure development levels in the country has transformed the playing field.
Today's consumers are more interested in personalised products of higher quality with better safety features at a competitive price. The marketplace has no room for flaws in quality, especially at a time when massive recalls are rattling even the biggest brands.
The only way for manufacturers in India to manage growing product complexity, maintain quality assurance and competitive costs is to take advantage of the boom in global and technological advancements. Recent statistics suggest that this fact is not lost on manufacturers in India. Robot installations in India grew 23 percent in 2013 from the previous year, with annual sales hitting a record 1,900, the latest figures available from the International Federation of Robotics.
That's just a fraction of China. About 56,000 units were sold last year alone in the world's biggest robot market, where factories including iPhone producer Foxconn Technology Group are helping China keep its manufacturing edge against lower-wage rivals. To expand its manufacturing base, Foxconn is developing robots, and looking at setting up factories in India.
Today, shopfloor tasks commonly performed by industrial robots include welding, painting, polishing, deburring, assembling components, transporting items and machining. The new generation of robots is increasingly able to understand their surroundings better through sight and sound systems and can distinguish between different components, even work alongside human beings.
To sustain successful robotic applications, shop floors need well-trained and highly skilled engineers to operate robotic simulation processes, offline programming and robot maintenance. The successful implementation of robots can help in visualising and predicting operational results with a heightened degree of certainty. Not to mention increased job satisfaction for employees due to smart, efficient and accurate results.
In addition to robotic installations on the shopfloor, factories are implementing several other automation models by employing programmable logic controllers (PLC). PLCs help in controlling robots, machinery, equipment, switches and alarms - they manage data communications among these elements to minimise human intervention, hence reducing human errors.
The virtual commissioning model, in which factories replicate the behaviour of a physical manufacturing environment with a software system, has numerous benefits for manufacturers including savings in labour, energy costs and improved product quality, accuracy and precision.
(Continued on the next page)