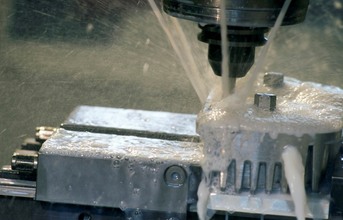
Thomas Kelm, Peter Köhmann's right-hand-man, is in charge of CNC programming and production. "Originally, we were using subcontractors to make parts," he says. "Quality and delivery were patchy, to say the least. Out of the blue the company who made the parts for us went out of business. Peter hired the owner and we bought a Haas VF-3 CNC machining centre."
"Our supplier had been working for himself for around 25 years," Peter adds, "so he found the transition very hard. Suddenly, he had a boss! "He began with us by working normal workshop hours, which he didn't enjoy. Immediately, he was very frustrated, so programming the Haas and setting-up the parts to be machined was laborious for him. He was using manual data input for all parts, irrespective of how complex they were. The quality of the parts he was making was not very good. So, Thomas began helping."
The new recruit lasted just a few days. One day, not unexpectedly, he didn't turn up. "In his absence, Thomas got the machine running and making parts. Our employee came back a day or two later to find Thomas was machining the parts. He decided there and then that he couldn't work for us. He found it too difficult to adapt and be part of someone else's company."
Thomas taught himself to use SolidWorks and CAMWorks. "I'm more of an ideas man," says Peter. "I sketch my ideas and Thomas now makes them into CAD models and generates the code. We found ourselves in a position where we could finally make the parts I was imagining. We were able to develop them, refine them and get them into production quickly. Parts that our subcontractor was making as fabrications, we were able to machine from solid billets, so they looked and worked so much better."
The mount for a rear disc brake, for example, was originally made on two machines: first a lathe, then a vertical. Now the part is made in one set-up on the Haas.