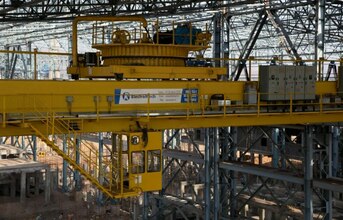
Furnace and rolling mills: The second phase of the entire process consists of furnace and rolling mills and includes handling of long metal billets of an average length of 12m each. The process is initiated by passing the billets on to idle rollers installed besides the furnace. The rolling facility is spread over 200m length and the preheated billets are passed through various horizontal and vertical rolling mills to give them the desired shape. The dies of the presses are required to be changed frequently to suit the particular product to be rolled, which includes rolled angles, TMT bars, metal rods and I-beams.
Quenching and cooling: The final phase includes the dispatch of the finished products. The despatch yard is spread over an area which is 380m long and 50m wide. This consists of parking bays for trucks and a railway track for loading on railway carriages. The despatch area has to store and handle long rods and beams. Rotating crabs are used to control the angle of long metal bars and other similar components in the despatch bay.
The solutions
Steel melting shop: ElectroMech responded to BMM Ispat's challenge with some unique ideas. Detailed analysis, design iterations and trials resulted in an integrated solution that has proved to be foolproof, achieving the intended task swiftly. A total of 13 cranes were designed to handle the material through various processes right from the steel melting shop to the placement of bars and rods on railway carriages. In the steel melting shop (SMS) where billets are formed, a total of four cranes with rotating trolleys assist in the manufacturing and storage of the billets.
Two cranes of 20MT each covering a span of 32.8m and another two 20MT cranes with 27.2m span cover the manufacturing and storage of the billets before they are sent for further processing. Since these cranes are part of a process and in constant use, these are designed for class 4 duty. The ambient temperature in the steel melting shop is approximately 60 Celsius, requiring all the components of the crane to be able to withstand such high temperatures. Hence, a slewing wheel type of arrangement was selected to be able to work in this area. An air-conditioned cabin is also provided for the operator.
(Continued on the next page)