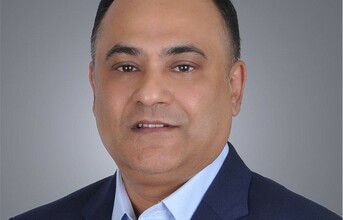
In a significant step towards digital transformation, Indofen Furnaces LLP, a premium manufacturer of advanced furnace systems for the aluminium recycling and die-casting industry, has adopted Siemens' Industrial Edge solution to modernise its operations. This strategic collaboration is helping Indofen unlock new levels of efficiency, sustainability, and scalability for its customers, setting a benchmark for the aluminium recycling and foundry sectors.
In an industry where fuel consumption, process variability, and unplanned downtime can impact profitability and environmental performance, Indofen's deployment of edge computing and real-time analytics has resulted in measurable gains in operational transparency, process control, and decision-making speed.
"Siemens Performance Insight provides our customers with a comprehensive view of furnace performance, including production data like metal charging and bale-out, fuel usage, and temperature, through real-time data, enabling operational transparency and swift, informed decision-making," said Ezhil Kumar, Managing Director, Indofen.
"Digitalisation is the key to unlocking the full potential of India's manufacturing sector. This collaboration is a strong example of how the Siemens Xcelerator portfolio is empowering India's small and medium enterprises to thrive in a digital-first economy. We are proud that Indofen has adopted our platform to make data-driven decisions, enhance productivity, and scale sustainably," added Suprakash Chaudhuri, Head of Digital Industries, Siemens Limited, India.
Siemens Performance Insight is part of the Siemens Xcelerator portfolio—an open digital business platform that accelerates digital transformation across industries. For the aluminium recycling and foundry sectors, where energy intensity, quality control, and process consistency are critical, the solution offers a clear path to sustainable and profitable growth.
Key Benefits for the Aluminium Recycling and Foundry Sector:
- Operational Transparency: Real-time monitoring of furnace parameters such as fuel usage, metal charging, and temperature ensures better control and output consistency.
- Energy Efficiency: Data-driven insights support reductions in fuel consumption and emissions, aligning with sustainability goals and regulatory compliance.
- Reduced Downtime: Predictive analytics and performance alerts minimise unplanned stoppages, enhancing throughput and extending equipment lifespan.
- Scalability: Modular digital solutions allow businesses to scale operations efficiently without compromising quality.
- Regulatory Compliance: Enhanced traceability and reporting simplify adherence to environmental and safety standards.