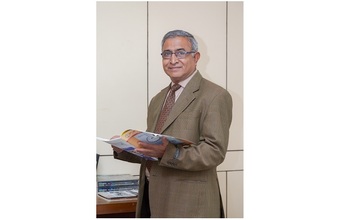
Tell us something about your manufacturing footprint and capabilities for both extruded products as well as for rolled products.
Jindal Aluminium Limited (JAL) is India's largest aluminium extrusion company having an inheritance that spans over 50 years. Started in the year 1968, the company's primary business is manufacturing of aluminium extruded and flat-rolled products. The company has a turnover of Rs.30 Billion (US$ 435 mn) with a production of above 1.25 lac ton in the FY 2018-19. Jindal Aluminium Limited leads the aluminium extrusions market in the country and is one of the foremost companies in aluminium flat- rolled products in India. Apart from India, the company exports to 42 countries across the globe.
Presently, Jindal Aluminium Limited has about 30 percent share in the domestic market. It has more than 80 distributors for extrusion and 29 dealers for rolled products. With a wide range of aluminium alloys in its manufacturing range, Jindal Aluminium Limited is the primary choice of customers ranging from various segments like architecture, aviation, defence, auto, electrical, electronics, engineering, façade, and solar to name a few.
Jindal Aluminium Limited's vision is to become the major supplier of quality aluminium extrusions and rolled products in the international market. The longstanding objective of the brand is to supply to its customers both in the national as well as a universal market with a product at a price, which to them embodies value, and is being delivered in a manner that surpasses their expectations.
While metrics like productivity and efficiency play a key role within a manufacturing organisation, what the customer values most is quality. What system does your organisation follow to ensure the quality of your products? What are the highlights of this system?
At Jindal Aluminium Limited, we lay a lot of emphasis on maintaining and improving our product's quality. In order to deliver customers with first-rate products without compromising on the quality factor, we have incorporated advanced equipment within our manufacturing unit: Below-mentioned are the highlights of these equipment:
Batch type Homogenizing Furnace for better finish and quality: Jindal Aluminium Limited has introduced batch type homogenizing furnace to refine the quality and finish of the products. With the enhanced homogenizing and correct microstructure of aluminium logs the surface finish of the aluminium profiles has majorly upgraded, which has resulted in scratch free products.
Intensive Cooling System to produce defect-free material: For all our round rods and critical profiles, we have an onboard high-tech intensive cooling system in our presses. This helps in producing the profiles without any distortion and deformation but also condenses our secondary solution treatment requirements to achieve good mechanical properties and hardness during extrusion itself. This has in turn helped to recover the product quality enabling us to produce defect-free materials.
Tunnel Furnace for uniform heating: We have introduced sophisticated automatic tunnel furnaces for heating the logs during the process of aluminium extrusion. Since these furnaces have a very good temperature controlling system and uniform heating system, we are able to extrude the material without any defects and with a better finish.
Polyurethane Rollers in place of PVC Rollers: On our finished extruded material handling conveyors, we have introduced Polyurethane rollers that have assisted to transfer the material with no scratches and roller marks, which in turn have upgraded our product quality.
Tell us about some of the advance manufacturing technologies used in your manufacturing plant/s. Tell us how these technologies are helping you in terms of productivity and overall efficiency.
To augment our productivity and to increase efficiency, we have been adopting and introducing the latest technology for the best operating efficiencies. Some of them are enumerated below:
Introduction of tunnel furnace: In order to heat the logs in our plant equivalently with a very close temperature, we have introduced tunnel furnaces in our extrusion presses. . This has enabled the company to generate defect-free extrusion with an enhanced finish with optimum productivity.
Refining the hydraulic oil quality: For the purpose of online cleaning of hydraulic oil, we introduced a cutting-edge oil filtration system, which abridged the levels of oil adulteration to a great degree. It has helped us to reduce the breakdown owing to the failure of a sophisticated hydraulic system due to oil contamination. It has also abetted us in running the plant unceasingly without any breakdown, which in turn has added value to our productivity.
Intensive cooling system: By introducing this innovative technology, it has assisted us to reduce secondary correction by manufacturing defect-free material with preferred mechanical properties. Because of this, we are able to produce superior quality products without performing any recurrent correction work. Additionally, these technologies have majorly contributed in saving our manpower and additional manual processing.
There is an increasing pressure on manufacturers to keep their prices competitive in the face of a bad market and intense competition. How are you reducing costs at the shop floor level?
Comprehending the current market conditions and the intense competition prevailing in the industry, JAL has undertaken the following steps to retain our competitive edge:
Increasing the breakthrough pressure: By surging the breakthrough pressure, we are capable to extrude most of the profiles at a much faster speed. The art is that productivity should be just optimum, as a very high productivity may distort the extrusion. This is where our experience of 50 years comes in handy.
Very low plant breakdown: Our plant breakdown is one of the lowest in the industry. We have been able to reduce it by ensuring that all the important parts of the plant are checked periodically so that our presses function seamlessly without any failure. The proper alignment of mechanical parts coupled with the continuous functioning of the press with no breakdowns has resulted in a higher productivity level and reduce our operating cost.
Shortening dead cycle time: After monitoring the hydraulic process, we have marginally revised the hydraulic circuit by diverting unused oil of the press to be used to reduce idle press speed which has amplified press speed and abridged the total dead cycle time, the end result being better production.
Upgradation of the quality of water: By maintaining good water quality with unceasing purification and the addition of beneficial chemicals to evade the formation of algae, we are able to maintain water quality which is utilised for the purpose of cooling hydraulic oil in the press. This supports us to improve and preserve the temperature of the oil and curtail failure of hydraulic components.
How do you perceive the role of your supply chain partners? What are your expectations from them?
We have a network of distributors, retailers, who play a crucial role in making our product available throughout the country and meeting the demand of the end-consumers.
Supply chains all across the globe are becoming instantaneous in movement and innovation. Hence, adding a competent supply chain partner can surely lend a company powerful and a planned leverage to meet novel trends and customer demands without having the need to make substantial infrastructure investments. While planning to get associated with a supply chain partner, we put a lot of importance on factors like the distributer's and retailer's ownership and location. This is because depending on the location they operate; we estimate if our company has a demand in that particular region and also gauge if we strategize to have any plans of expansion in those markets. We undertake a proper cultural understanding of how business is executed wherever our partner is based. We also expect our partners to be financially stable and they must be equipped with disaster recovery plans, cash-on-hand, footprint estimates, sourcing areas and costs, and customer concentrations. Comprehending these factors enables us in adding utmost value to our partnership.
Where does ‘Safety' feature in your priority list?
The aspect of safety is of paramount significance for us and is one of the top-most priorities. Jindal Aluminium Limited has been following all the safety norms and guidelines without any compromise. All our aluminium plants are absolutely free of any hazards and on an everyday basis with tonnes of aluminium are safely melted, casted and extruded. The company has a vigorous management system framework which ensures safety consciousness through sound safety measures, process safety management and an integrated emergency response. Our security and prevention measures are directed towards safeguarding the health of our employees, contractors and site workers, thus ensuring there are no fatalities. By continuously advancing our cautionary practices we safeguard to control and mitigate potential health hazards.
Due to growing environmental awareness, manufacturers are working towards converging economic and ecological objectives at the production and logistics levels. Tell us about this in the context of your manufacturing operations.
The company strives hard to abide to the environmental guidelines and follow ecological practices at our production and logistic level. Mentioned below are a couple of sustainable strategies that are followed in our manufacturing operations:
Conversion of the furnace from oil to gas: Initially, our furnaces were running with FO & LDO, which have been converted to LNG. This conversion has not only condensed our pollution level but has also reduced the ambient temperature in our plant and neighbouring areas. Additionally, our cost of production has also been cut down since the gas requires no atomizing, which has helped in reducing the power consumption value.
Automatic storage and transfer system: We have introduced an automatic vertical log storage system for the purpose of storing the logs for extrusions. This has enabled us to store the logs vertically. Along with saving a lot of storage space, the automatic storage and transfer system have helped us to shrink manpower.
Upgrading the performance of melting furnace: We have altered the refractory material in the furnace with superior quality one, which helped us to run the furnace unceasingly for about 6 to 9 months' time. Along with reducing the breakdowns of the furnace, it has also reduced our needless maintenance and saving of time and materials. This further contributes towards saving a lot of manpower and materials. Additionally, our production cost and fuel consumption have also been reduced majorly.
END