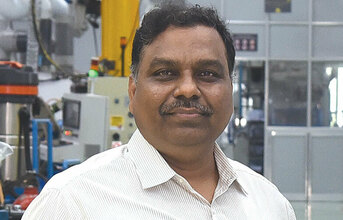
How would you compare the Production Unit Pune Round Tools with Sandvik Coromant's similar units around the world?
This is first multi-storeyed manufacturing facility at Pune site. Pune Round Tools production unit is one of the best production units in the world having highly automated state-of-the-art manufacturing machines and equipment, benchmark processes and system as well as qualified staff and competent people. It is a global supply unit that manufactures and supplies standard, tailormade and special solid round tools with world class quality, on time delivery at high productivity and optimum costs by implementation of lean best practise.
What are the green initiatives and safety measures implemented in the plant?
Coromant has high commitment towards sustainable planet and there are many green initiatives implemented in the plant. The building is designed to illuminate using natural day light and LED lamps. It is ventilated with evaporative ventilation system than air conditioning.
It has 100,000 litters sump used to harvest rain water which is used in processes and recycled again. Same water sump is used to cool the heat treatment furnaces rather than using chillers thereby reducing electricity consumption and improving energy efficiency. It also helps to conserve scarce water resources.
The plant and machinery are protected against risk of fire using dry type transformers, smoke detectors, automatic fire extinguishers, and sprinklers. The site is certified as highly risk protected site by FM Global.
What are the various tools manufactured at this Unit and what is the overall capacity of this facility?
The plant has annual capacity to produce nearly 2.5 million solid round tools and is currently producing more than two million tools per annum. The plant manufactures high tech HSS Taps including those with powder metallurgy substrate, Solid carbide drills, endmills, reamers and provides reconditioning and recoating services for these tools. The tools are used in different sectors such as automobile, aerospace, oil and gas, energy, die and mould and general engineering for drilling, milling, reaming and tapping operations on wide range of materials with optimised performance.
Tell us something about the development of Coro TapTM, the new product launched from the Pune Production Unit. Tell us about the overall new product development activities at this Unit.
Pune unit has moved upward in global supply chain and is working closely as a master unit with R&D and product management. It has engineering and manufacturing capabilities to introduce new products and processes, make prototypes and do extensive trail and testing for optimization of new products before introduction. Our Unit has so far launched various new products such as Corotap-XM, ISO-K, ISO-N taps and development of few more new taps is ongoing. These are application taps with optimised geometries, substrates and coatings to provide solution to varied machining applications.
How do your engineers help your customer in choosing the right kind of tools for their requirements?
Our trained and competent design engineers support our customers via "Enquiry management system and CAPP" to provide solution for special applications.
Digitalisation of production is a major trend all over the world. How has your Unit adopted it? How easy or difficult is it to maintain balance with production costs?
Digitization is going to change how we design, manufacture and use our products in big way in days to come and Coromant has proactively started its journey to lead this change within its production. We have completed digital diagnostics of our manufacturing operations and will continue our journey of reducing waste and optimizing efficiency and productivity with digital tools and initiatives. We are focusing our efforts on key pillars such as cyber physical equipment, connected systems, data analytics and digitized visualization for better performance management. For example, we have already initiated IOT projects such as Coroplus process control on our machining centres to improve its safety and uptime and use of Cobots with pick and place automations in our production. We are also using CAPP for seamless planning and scheduling of tailormade and special orders.
We have initiated the process to build digital competencies and develop necessary mindset and behaviours among our employees to embrace this change and make maximum out of it for all stake holders.
Cost competitiveness is vital to our business and we are wisely choosing and prioritising on those digital initiatives which would help us reduce waste, improve efficiency, productivity and increase utilization of our bottlenecks to be cost competitive.
I understand the Production Unit at Pune also offers reconditioning service. What kind of equipment and infrastructure do you have in this regard and how are you helping your customers with the same?
Reconditioning service is key value-added service provided to our customers as it reduces the effective cost of expensive solid round tools to half over its useful life. We have state-of-the-art 7-axis ANCA MX5 and Walter Helitronic CNC tool and cutter grinders for geometry grinding and Walter helicheck CNC measuring equipment for quality control of precision tools. We have the complete technological knowhow and competencies required to recondition and recoat our tools to the same original quality assuring life of new tools. Reconditioning is green and sustainability initiative which helps to reuse expensive tool minimum three times and scrapped tools are recollected and recycled by Coromant to conserve natural resources.
END