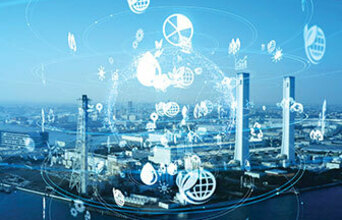
The reality of digital transformation is now all-pervasive. Over time, it has affected the manufacturing industry as well, forcing companies to make investments which enhance the "smartness quotient" of their factories. Industry 4.0 or Smart Manufacturing are terms that describe this development. To succeed in a particular market niche today, growth in terms of quantities and revenue is no longer sufficient. Understanding the latent needs of the customer and having the capability to address this with agility is a crucial factor to win in today's volatile market.
A DIGITISED SUPPLY CHAIN
The pandemic has created the opportunity for the implementation of digital technology in the manufacturing sector. Businesses that have been successful first-movers in thinking digitally find themselves relevant and expanding profitably. By making the best use of artificial intelligence, the cloud, and other platforms, they are solving complicated challenges in real-time, have greater insights and accessibility, and are becoming agile organisations. Covid 19 has presented opportunities for businesses in terms of global supply chains. Customer patience in terms of lead times is continuously shortening, and to handle supply within these constraints, information systems must be automated and digitalised, providing reliability of commitment, and transparency of progress to the customer.
Digital supply networks employ seamless, integrated technology solutions. This breaks down silos and improves communication among supply chain participants. They use automatically updated real-time information. This enables prompt reactions, facilitating organisations to identify problems or hazards well in advance. Digital warehousing solutions are provided through supply chain digitisation, where sophisticated warehouse management systems are used to communicate data in real time and expedite the fulfilment and shipping process.
SMART MANUFACTURING ENABLES SUSTAINABILITY
Digitalisation enables supply chains to move quickly, flexibly, and affordably. Along with improving the overall customer experience, digital transformation in supply chain management also benefits businesses as it provides insights into the functioning of the supply chain through data analytics, helping businesses to better plan the complete supply chain management. They also increase functional efficiencies through improved forecasting and complex problem-solving.
One can adjust production schedules by understanding the timeline of raw material supply with the aid of technologies like GPS tracking. Similar to how firms may simplify their operations effectively by using digital tools and technology, this is also true for supply chain management. Businesses may identify and address problems or uncertainties at any time with the use of real-time updates, assuring prompt delivery of finished goods or raw materials. They can utilise data to enhance visibility so that the business has the best possible understanding of demand, inventory, capacity, and supply throughout the ecosystem.
MAKING THE WHOLE CHAIN SMARTER
It is truly said that competition now is not between companies but their supply chains. Smart manufacturing is but the starting point in the digitalization of a manufacturing business. To leverage the benefits of smart manufacturing, it is essential to enhance the smartness quotient of the end-to-end supply chain. A major success factor for a business is the customer experience, and in a manufacturing business, it is all about quality, delivery, and price, coupled with reliability/predictability and transparency/trackability (the latter a customer expectation which has been whetted by the same being provided by e-commerce giants).
At Godrej & Boyce, we took small steps in the journey as long as a decade ago, using sensors on legacy equipment (a "brownfield" project) to gather data to monitor and control process parameters. This gave us control of quality assurance as well as insights into condition-based maintenance. These baby steps prepared us to take our next bold steps into smart manufacturing as opportunities for greenfield projects came our way with the company's aggressive growth plans fuelled capacity enhancement.
The next phase of working towards a smarter supply chain included bringing the voice of the customer directly on the shopfloor removing the possibility of errors of transmission/translation, and at the same time automating the progress of components through the factory floor in a manner which served the dual objectives of enhancing our ability to customise products as per the needs of individual customers while optimising capacity utilisation.
Bringing suppliers and business partners on board with "appropriate automation" through scalable automation of processes rather than a big bang approach then helped bring all the elements of the end-to-end supply chain on a common platform from where all can progress together.
MAKING MANUFACTURING BETTER AND CLEANER
It's not only about efficiency when it comes to smart manufacturing. Businesses that embrace smart manufacturing end up lowering their carbon footprint by cutting waste, but sectors that use a lot of energy stand to benefit the most from energy savings because they will not only decrease energy waste but also lower costs for goods.
To keep up and remain competitive, manufacturers of all sizes must strive toward smart manufacturing. Embracing smart manufacturing begins with the leadership of a company. The first step is to make equipment investments with an eye toward scalability in integrating smart manufacturing. This will eventually enhance the procedure, provide cost savings, and boost sales.
For the manufacturer, service provider, and end-user throughout the value chain, a linked supply chain provides optimization and cost savings. Manufacturers can switch to just-in-time manufacturing, in which items, labour, and resources are planned to arrive or be replaced precisely when needed in the production process. This enables the producer to switch to demand-based manufacturing and avoid expensive excess. When linked machines indicate what they need and when they need it, optimising parts ordering, inventory management, and replacement is simpler for the customer and service provider. By doing this, both the client and the service provider may increase customer happiness. Thus, the time has come to embrace smart manufacturing at every operative point for the business. This is the future, and the future is already here.