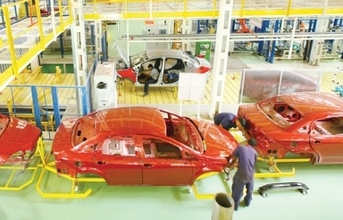
In manufacturing, supply chain planning has primarily been based on forecasts, commitments made by the sales team or growth targets. However, there may be significant difference in the demand pattern of each product category while the manufacturing processes / stages may be similar.
For example, rainfall patterns, water table levels, soil conditions etc. determine the type of agro-chemical or pump to be produced. An extension of the summer season changes the demand pattern for certain consumer products such as air conditioners and fans.
A sudden outbreak or increase in a certain disease in a particular geography impacts the demand pattern for pharmaceutical products. Competitor move or strategies also impact the demand or sales pattern. Given these situations, planning in the supply chain becomes a trigger based process reacting to market changes and organisations often tend to adopt a ‘One size fits all' approach.
This approach may impact organisations in terms of 1) not being able to meet customer schedules and therefore revenue / margin targets, 2) higher inventory levels (as the right products are not being produced) and 3) lower levels of plant utilisation. To put it plainly, while manufacturing capacity is available and inventory levels are high, organisations are still unable to deliver the right product to the customer on time.
In the drive to enhance efficiencies, organisations tend to reduce focus on flexibility. This has often led factories to schedule large batch runs (leading to blocked capacities) and hence delays in reacting to customer / demand changes. In other words, efficiency means longer batch runs in the shop-floor, lower number of product varieties and less disruption to production plans.
While efficiency is key, flexibility is important to address changing market conditions which drive profitable growth. In view of this, organisations are looking at differentiated planning models across product categories rather than adopting the ‘One size fits all' approach and move from a homogenous system to a heterogeneous system.
Variability in demand |
Volumes |
Strategy to be deployed |
Low |
High |
Produce standard quantities for a defined period |
High |
Medium |
Stock parts and assemble based on order |
High |
Low |
Produce based on order |